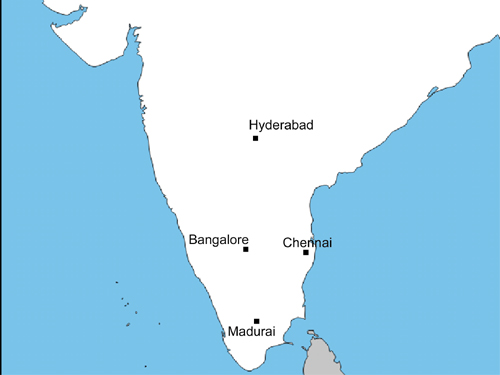
The Bangalore to Hosur route is a well worn one, known to all who stone importers and buyers of granite slabs and tiles from India, and those who are part of the accessory industry supplying machines etc. This corridor is now well established and well known for its high quality premium slabs factories which are second to none in the world in production and management systems. The production in the modern gangsaws and blockcutters factories in the Bangalore area is estimated to be around 6 million sq metres in early 2014. If the production of granite tiles from the hundreds of cheap and rudimentary single disk block cutters is also included, total production would be at least an additional 6 million sq metres.
For years this is the place where stone importers have found it convenient to go and prefer to go. Bangalore is a cosmopolitan city with all the facilities one ask for in terms of convenient flights, hotels, etc. Unlike the Spanish industry there was no collapse in the local market when the financial crisis struck in 2008. On the other hand, demand in the local market actually increased substantially in this huge country of 1.2 billion people, and economic growth in India remained very strong in the first 4 years of the crisis. However, the Bangalore based industry being principally export oriented, was seriously affected with the sharp decline in demand in the US market, the main destination of Indian slab exporters. After a turbulent period of about a year in which no one went bankrupt though everyone was seriously shaken, the Indian industry recovered strongly on the back of fast growing demand in the emerging markets all over the world.
One significant difference between the two centres located in different continents was this- when the financial crisis began, the Spanish stone industry was overly dependent on the local market with an over the top building boom that collapsed suddenly and there some which exported nothing. These were the companies that, by and large, disappeared. The Bangalore based cluster depended and still does, mostly on the export markets, especially the US market, though it is far more diversified now in terms of geographical markets.
The surviving industry in Galicia depends on the easy availability of a fairly large variety of quarries of in its vicinity. While not as evident, one of the unmentioned foundations of the development of the industry in Hosur was its easier access to the premium materials, of which the quarries are located in the Madurai district (Kashmir White etc.) The Bangalore industry also had easier access to the materials quarried in the state of Andhra Pradesh and the processing capacity in that state was limited, till recently.
The big problem for the Bangalore based industry actually came in the form of a man made crisis when in mid-2012 almost 200 quarries located in the Madurai district were suddenly shut down by the local government due to alleged irregularities. These quarries are still not operative. This closing down of so many quarries exposed the Achilles Heels of this industry. Many of the factories in the Bangalore cluster are owned and run by people who do not have their own quarries. This was not considered a relevant factor as long as the factories were able to purchase the blocks from the quarries located in Andhra Pradesh and Tamil Nadu apart from the ones in the states of Karnataka. But once the granite processing industry took off in Andhra Pradesh, suddenly popular materials like Black Galaxy, Tan Brown etc. were not so easily available to these factories, it made more sense to process them in the factories located close by.
While the Bangalore based industry has always been familiar with working with imported materials from Africa, the Nordic countries and even Brazil, the biggest problem now became the access of raw materials. Suddenly the block buyers from the companies were to be found all over the world marking blocks and competing ferociously for raw materials with the Chinese and European factories, and among themselves. Due to the higher transport costs, the long time cycle of more than 6 months between making payments for the blocks and collecting money from their clients for the finished product, the biggest challenge for many now became how to meet the vastly higher working capital requirements. In a country where money is expensive, the big challenge for the processing factories towards end of 2013 was how to avoid debt and maintain an acceptable level of profitability in a market which is very competitive due to the large number of factories located in the area. The debt level of a company is a key factor. The need to keep the gangsaws and blockcutters working means there is even greater pressure to get access to the really top of the line high margin granites, be they from Brazil or Norway, or elsewhere. On average between 30 to 50 % of the blocks being processed currently are imported when previously the amount was 10 to 25%.
With processing facilities having reduced in size dramatically during the last decade in Europe (processing in Europe is estimated to be around 12-15 sq million equivalent now as against almost 40 million sq metres 10 years ago), granite processing is now basically concentrated in China, India, Brazil and Saudi Arabia. With Saudi Arabia focused almost entirely on the local market, and the Chinese industry in a state of transition adjusting to a reduced local market and a higher cost economy, the road forward continues to look promising for the Indian industry. It has a huge domestic market to sell to and the whole world too. In other words, lack of demand is not seen as a major problem, either in the short run, or in the medium and long term.
While the future may well be bright the short term prospects continue to look uncertain for at least some companies. The daily struggle to obtain raw material and not lack of demand for one´s products as being identified as the main problem, is a unique situation, not very common, in most industries, anywhere in the world.
The logical thing is to expect that one day not too far in the future the Madurai quarries will reopen and the blocks from these quarries will be back in the market. Help may be around the corner though. New quarries are now opening in the not so far away Sivakashi and Tuticorn area- the granites from these areas tend to be cream, gold and white in colour- in other words, materials with wide demand everywhere. Now the products offered by the factories go by the different names - Colonial Ivory, Colonial White, Gold Chiffon, etc. So high is the demand that prices of blocks have almost doubled within a year and the quarries cannot produce enough of them. But the high margins earned by the quarries also means the quarry operators are making big investments in increasing production. In other words, while slow administrative decision making in resolving the problems of the Madurai region quarries has caused serious damage to a major employment generating industry, market forces and plain and simple entrepreneurship are once again promising to bring back the luster to the Bangalore based industry.
The shortage of blocks will, however, probably continue to be a constant problem. In the end the issue boils down to many factories all trying to get hold of the same high quality blocks for which there is high demand. As anyone with a minimum knowledge of the stone quarrying industry knows, almost by definition, the supply of these blocks will be limited- there will always be a shortage.
One great puzzle is why has the Indian granite industry not moved on to the next stage of sophistication- that of doing cut to size and more sophisticated stone processing? Logic dictates that with the experience of over two decades, pushed by competitive pressures and with an eye on exploiting opportunities, there would by now be several Indian companies specializing in cut to size projects. This segment of the market, which requires a different set of skills, still remains relatively unfilled, with only a handful of companies in India doing complex projects. Perhaps it is a matter of time, but the evolution to this segment of the industry is now long overdue.
The Bangalore based industry could also demonstrate more innovation, at the end of day, the manufacturing industry is basically a supplier of slabs for the kitchen counter-top market in the United States, at least to the extent of almost 40 to 50 % of its production. One still sees too few new and different kinds of finishes, and there has been practically no attempt to develop new applications for stone and to create entire new industries based on natural stone. Being one of the principal and most sophisticated granite processing industries in the world, the Bangalore based granite industry should be assuming a leadership role in this area. This is, after all, the unspoken responsibility of a cluster which occupies a top rank, it should feel the pressure to be highly innovative. Yet there is not enough talk of these issues, at least not yet. The quarry owners too need to make serious efforts in resolving the problem of relatively low recovery and will have lower wastage, perhaps in collaboration with the processing units. There is much scope for this kind of collaboration.
The focus on efficiency and factory organization, a hugely admirable trait requiring constant and obsessive attention to details, have been the hallmarks of the leading Bangalore based factories, and have made them highly respected world leaders. All the more so in a country like India which is usually far too tolerant of mediocrity. But it is not enough anymore. The industry simply has to climb up the next steps of evolution or risks being caught up and left behind by other granite processing areas.
Overall, though, despite the loud and constant complaining of so many daily hurdles and problems in doing business, unique to India, because they are unthinkable in the developed world, or even in China, one still leaves the place optimistic about its future. The dynamism, the energy and sheer entrepreneurship are infectious. Watch this space. We will be back soon to cover it again.
Sections